Discover the Essential Role of Stainless Steel Banjo Fittings in Modern Applications
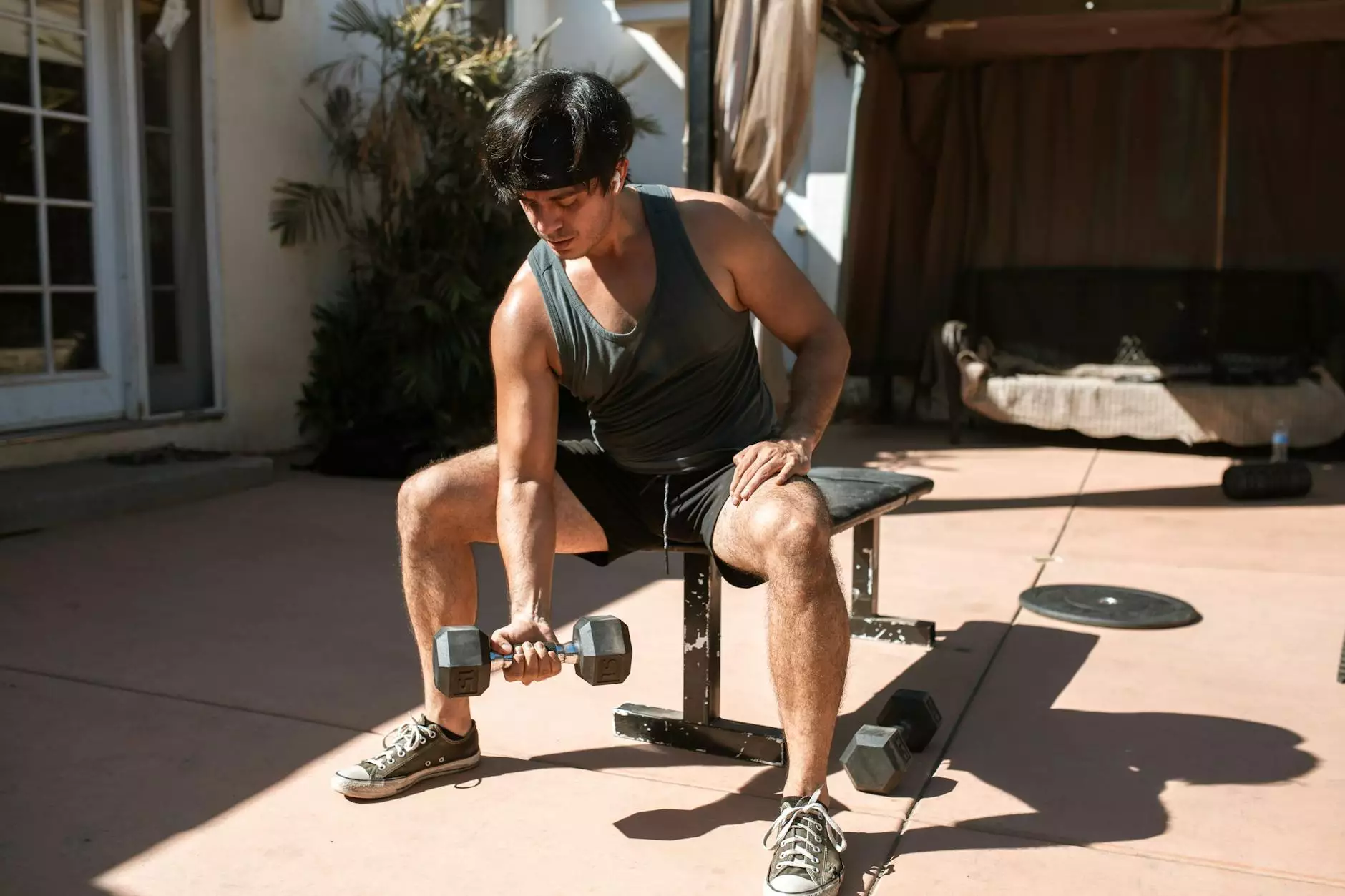
In today's fast-paced industrial environments, efficiency, safety, and durability are paramount. Among various components that serve these purposes, stainless steel banjo fittings have emerged as a crucial element in different applications, particularly in the automotive and hydraulic sectors. This article delves deep into the world of banjo fittings, their unique benefits, applications, and the factors to consider when selecting the right fittings for your needs.
What Are Stainless Steel Banjo Fittings?
Stainless steel banjo fittings are specialized connectors designed to facilitate fluid transfer in a variety of systems. These fittings feature a unique design that enables them to connect pipes and hoses at various angles, optimizing space and fluid flow efficiency. Made from high-quality stainless steel, these fittings are resistant to corrosion and high temperatures, making them suitable for various challenging environments.
The Composition of Stainless Steel
The durability and performance of stainless steel banjo fittings significantly depend on their composition. Typically, stainless steel is an alloy composed of iron, carbon, and a minimum of 10.5% chromium. The presence of chromium forms a passive layer of chromium oxide on the surface of the steel, which protects it from rust and corrosion. Common grades of stainless steel used in banjo fittings include:
- 304 Stainless Steel: Offers good corrosion resistance and is often used in food and beverage applications.
- 316 Stainless Steel: Provides enhanced corrosion resistance, particularly against chlorides, making it ideal for marine environments.
- 321 Stainless Steel: Known for its excellent stress corrosion cracking resistance and high-temperature performance.
Applications of Stainless Steel Banjo Fittings
Given their robust design and reliability, stainless steel banjo fittings are used across various sectors, including:
1. Automotive Industry
In vehicles, these fittings are commonly utilized in hydraulic brake systems and fuel lines due to their ability to withstand high pressure while ensuring leak-free connections.
2. Aerospace Sector
With rigorous safety standards, aerospace applications benefit from the lightweight nature and strength of stainless steel banjo fittings, which help reduce overall weight without compromising integrity.
3. Marine Applications
The resistance to saltwater corrosion makes stainless steel banjo fittings an ideal choice for boats and ships, ensuring long-lasting performance in harsh marine environments.
4. Industrial Machinery
From hydraulic lifts to assembly line machinery, these fittings are critical in ensuring efficient fluid transfer, contributing to the overall performance of industrial equipment.
Benefits of Stainless Steel Banjo Fittings
The advantages of utilizing stainless steel banjo fittings in your projects are numerous:
1. Corrosion Resistance
One of the standout features of stainless steel is its resistance to rust and corrosion, ensuring longevity, especially in environments exposed to moisture and chemicals.
2. High Strength
These fittings maintain their integrity under high pressure and temperature, which is essential in applications like hydraulic systems where reliability is critical.
3. Versatility
Stainless steel banjo fittings can be configured in various angles and sizes, making them suitable for countless applications across different industries.
4. Low Maintenance
Unlike other materials that may require regular maintenance or replacement, stainless steel minimizes upkeep costs due to its durability.
5. Aesthetic Appeal
Beyond functionality, the sleek finish of stainless steel fittings also adds an element of visual appeal, especially in visible installations.
Choosing the Right Stainless Steel Banjo Fittings
When selecting the appropriate stainless steel banjo fittings for your application, consider the following factors:
1. Compatibility with Fluids
Ensure that the chosen fitting material is compatible with the fluids being transferred to avoid any chemical reactions that could compromise the integrity of the system.
2. Pressure and Temperature Ratings
Verify that the fittings can withstand the specific pressures and temperatures they will experience in their intended use.
3. Size and Configuration
Select fittings that match the size requirements of your pipes or hoses, paying attention to the needed configurations to facilitate effective installation and operation.
4. Installation Considerations
Evaluate the ease of installation of the fittings in your system, along with any necessary tools or hardware required for a secure connection.
5. Vendor Reputation
Source your stainless steel banjo fittings from reputable suppliers like fitsch.cn, ensuring quality and adherence to industry standards.
Installation Tips for Stainless Steel Banjo Fittings
The installation process of stainless steel banjo fittings is fairly straightforward, but certain best practices can help ensure a successful setup:
- Clean the Surfaces: Before installation, ensure that both the fitting and the connecting surfaces are clean to avoid contamination that may lead to leaks.
- Use the Right Tools: Utilize appropriate tools to tighten the fittings properly. Avoid over-tightening, as this can damage the fitting or the connected components.
- Check for Leaks: After installation, test the system under operational conditions to check for any leaks and make necessary adjustments.
- Regular Inspection: Incorporate routine maintenance checks to monitor the condition of the fittings and replace them if any signs of wear or damage are detected.
Conclusion
In conclusion, stainless steel banjo fittings play a vital role across multiple industries due to their exceptional characteristics and remarkable reliability. Whether it's in vehicles, aircraft, or heavy machinery, their versatility and performance make them indispensable components. When sourcing or installing these fittings, prioritize quality by partnering with reputable suppliers like fitsch.cn, ensuring you receive the best products for your industrial needs. Understanding their advantages, applications, and installation methods will empower you to make informed decisions that enhance your operational efficiency and reliability.