Unlocking the Potential of Rapid Prototype Aluminum Casting
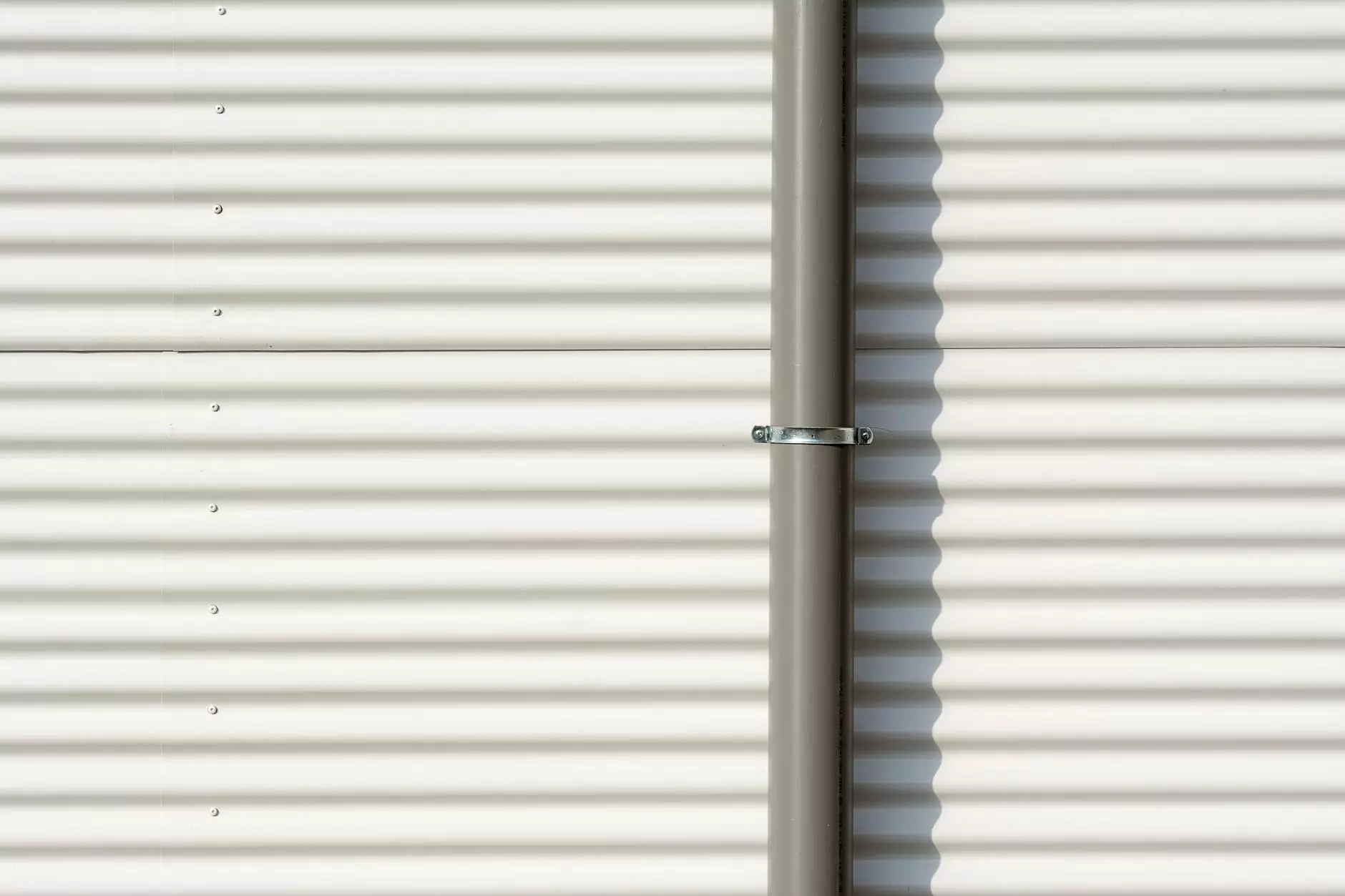
Introduction
Welcome to quickparts.com, the leading online platform for metal fabricators and 3D printing enthusiasts. In this article, we will explore the power and potential of rapid prototype aluminum casting, showcasing how it revolutionizes the manufacturing industry. Our goal is to provide you with comprehensive insights into the benefits, applications, and process of rapid prototype aluminum casting, helping you stay at the forefront of innovation.
Understanding Rapid Prototype Aluminum Casting
Rapid prototype aluminum casting is a cutting-edge technology that allows businesses to quickly and cost-effectively create high-quality prototypes and functional parts made of aluminum. This process utilizes 3D printing technology, also known as additive manufacturing, to produce intricate designs with exceptional accuracy and detail.
The Benefits of Rapid Prototype Aluminum Casting
- Speed: One of the major advantages of rapid prototype aluminum casting is its incredible speed. Traditional manufacturing methods often require extensive lead times, but with rapid prototyping, businesses can accelerate their product development cycle significantly.
- Cost Savings: By utilizing rapid prototype aluminum casting, businesses can reduce overall costs associated with tooling and production. This technology eliminates the need for expensive molds or dies, providing a more economical solution for small-scale productions or one-off prototypes.
- Design Flexibility: Rapid prototype aluminum casting enables designers to turn their visions into reality with unparalleled design flexibility. Complex geometric shapes, intricate details, and customized features can be easily achieved, opening up new possibilities for innovation.
- Material Properties: Aluminum, a widely used material in various industries, offers exceptional mechanical properties such as strength, lightweight, and corrosion resistance. Rapid prototype aluminum casting allows businesses to explore and test these properties in their prototypes before finalizing the production process.
- Time-to-Market: With rapid prototype aluminum casting, businesses can rapidly iterate their designs, leading to a shorter time-to-market. This gives companies a competitive edge in an increasingly fast-paced and dynamic business environment.
Applications of Rapid Prototype Aluminum Casting
Rapid prototype aluminum casting has found extensive application across many industries, revolutionizing product development and manufacturing processes. Some key sectors leveraging this technology include:
Automotive Industry
The automotive industry has greatly benefited from rapid prototype aluminum casting for creating prototypes, custom components, and even lightweight structural parts. This technology allows for faster development cycles for new vehicle models and facilitates the production of high-performance and fuel-efficient automobiles.
Aerospace and Aviation Industry
Rapid prototype aluminum casting plays a crucial role in the aerospace and aviation industry. By using this technology, engineers can create intricate parts that meet strict performance requirements while reducing weight. From airframe components to engine parts, rapid prototyping with aluminum has become a game-changer for the industry, promoting innovation and enhancing safety.
Consumer Electronics
Rapid prototype aluminum casting offers consumer electronics manufacturers an efficient way to produce prototypes and final products with exceptional precision. This technology enables the development of sleek, durable, and functional products, ranging from smartphones to wearable devices, that meet the ever-evolving demands of consumers.
Medical Devices and Healthcare
In the medical field, rapid prototype aluminum casting finds tremendous application in the manufacturing of surgical instruments, prosthetics, and medical devices. It allows for the production of complex, patient-specific designs that are durable, lightweight, and biocompatible. This technology greatly enhances the efficiency and effectiveness of healthcare solutions, leading to improved patient care.
The Rapid Prototype Aluminum Casting Process
The process of rapid prototype aluminum casting involves several steps, each crucial to achieving precise and high-quality results.
Design and CAD Modeling
Initially, the design concept is created using Computer-Aided Design (CAD) software. This digital model serves as the foundation for the physical prototype.
Material Selection
Choosing the appropriate aluminum alloy for the intended application is critical. Factors such as strength, thermal conductivity, and corrosion resistance are considered during this stage.
Pattern Creation
A pattern is produced using 3D printing technology based on the CAD model. This pattern serves as a template or mold for the final cast part.
Mold Assembly and Preparation
The pattern is then used to create a mold, which is typically made of a material like sand or ceramic. The mold is assembled and prepared for the casting process.
Casting and Finishing
Molten aluminum is poured into the mold and allowed to cool and solidify. Once solidified, the cast part is carefully removed from the mold and any excess material is trimmed and finished to meet the desired specifications.
Post-Processing
The final cast part may undergo additional post-processing steps, such as heat treatment, surface finishing, or machining, to achieve the desired properties and aesthetics.
Conclusion
Rapid prototype aluminum casting is a game-changing technology that empowers businesses to innovate, reduce costs, and accelerate time-to-market. Its versatility and countless applications across various industries make it an indispensable tool for manufacturers and designers. At quickparts.com, we offer a comprehensive range of metal fabrication and 3D printing services, including rapid prototype aluminum casting, to help you bring your visions to life. Stay ahead of competitors by leveraging this revolutionary technology and unlock a world of possibilities for your business.